Blow-Fill-Seal (BFS) Technology
Posted on JULY 12, 2022
A preferred packaging process for parenteral products
BFS is an advanced aseptic processing technology that is typically used for filling & packaging of sterile liquid formulations. It is an automated manufacturing process by which plastic containers are, in a continuous operation, get blow-formed, filled, & sealed. It takes place in a sterile, enclosed area inside a machine, without human intervention, & thus can be used to aseptically manufacture sterile pharmaceutical products.
Every BFS process begins with the extrusion of a sterile polymer parison directly within the system. Once complete, the container can then be moulded, filled, sealed, & demoulded, all in a single process, in a self-contained system, & without the need for any external intervention.
Blow-Fill-Seal - Five Principal Stages

EXTRUDING

BLOWING

FILLING

SEALING

DEMOLDING
Advantages:
- BFS offers a wide range of unbreakable & user-friendly containers in lots of shapes & sizes.
- BFS is a superior choice for highly sensitive formulations because it provides ISO Class 5 safety conditions.
- Fully automated processes for manufacturing, filling, & sealing containers in seconds (cycle time approx. 15 seconds).
- BFS containers are lighter than glass containers & they are also shatterproof, which eases their transportation.
- Due to the single-dose nature of BFS containers, they are more convenient to patients.
- Compared to other packaging processes BFS technology is inexpensive.
- BFS assures one integrated process without the need for human intervention.
- Transparent, completely collapsible, mounting brackets option, suitable for use with various cap/closure types.
- Outstanding filling accuracy.
- Tried & tested design, ensures product reliability.
Our BFS Product Range:
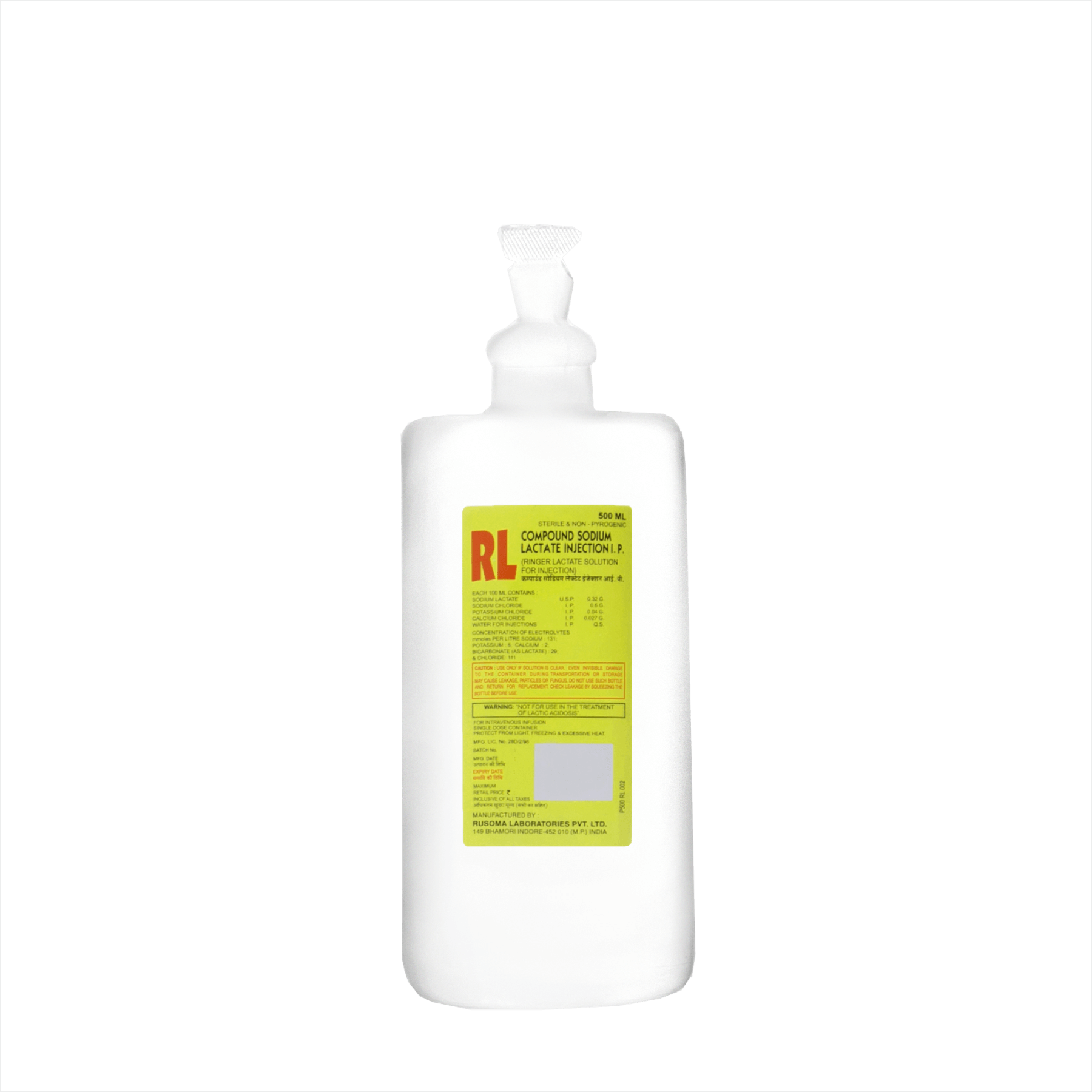
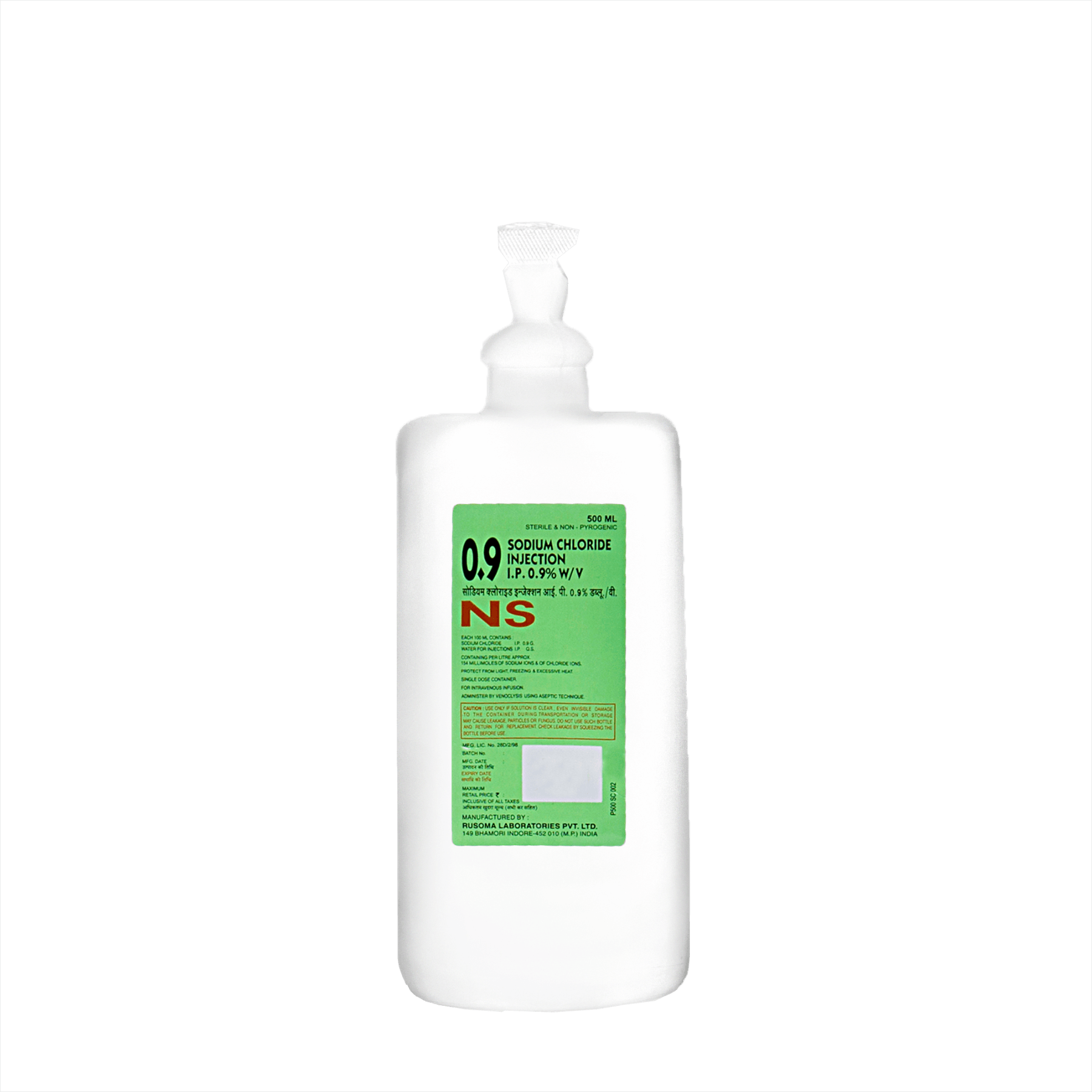
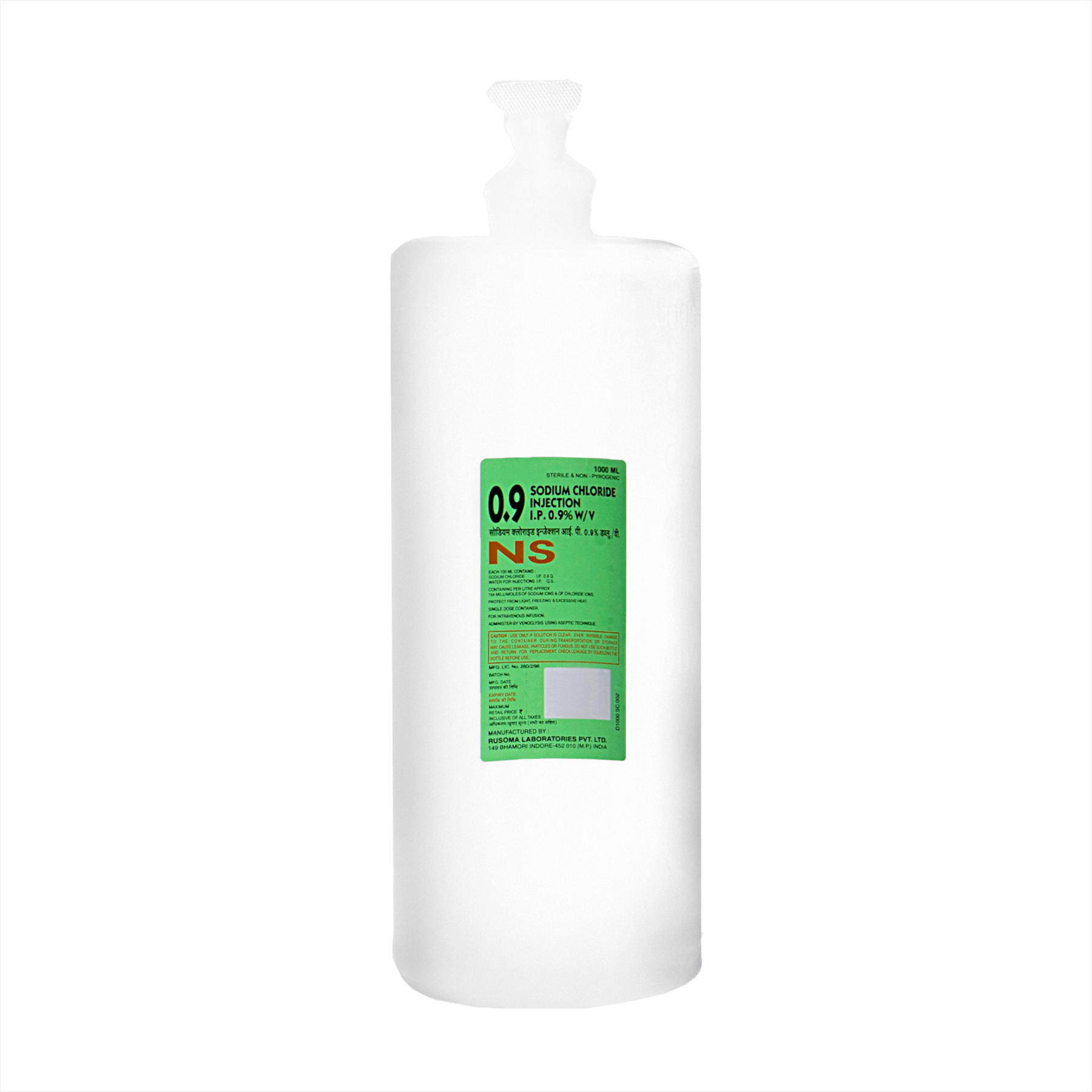
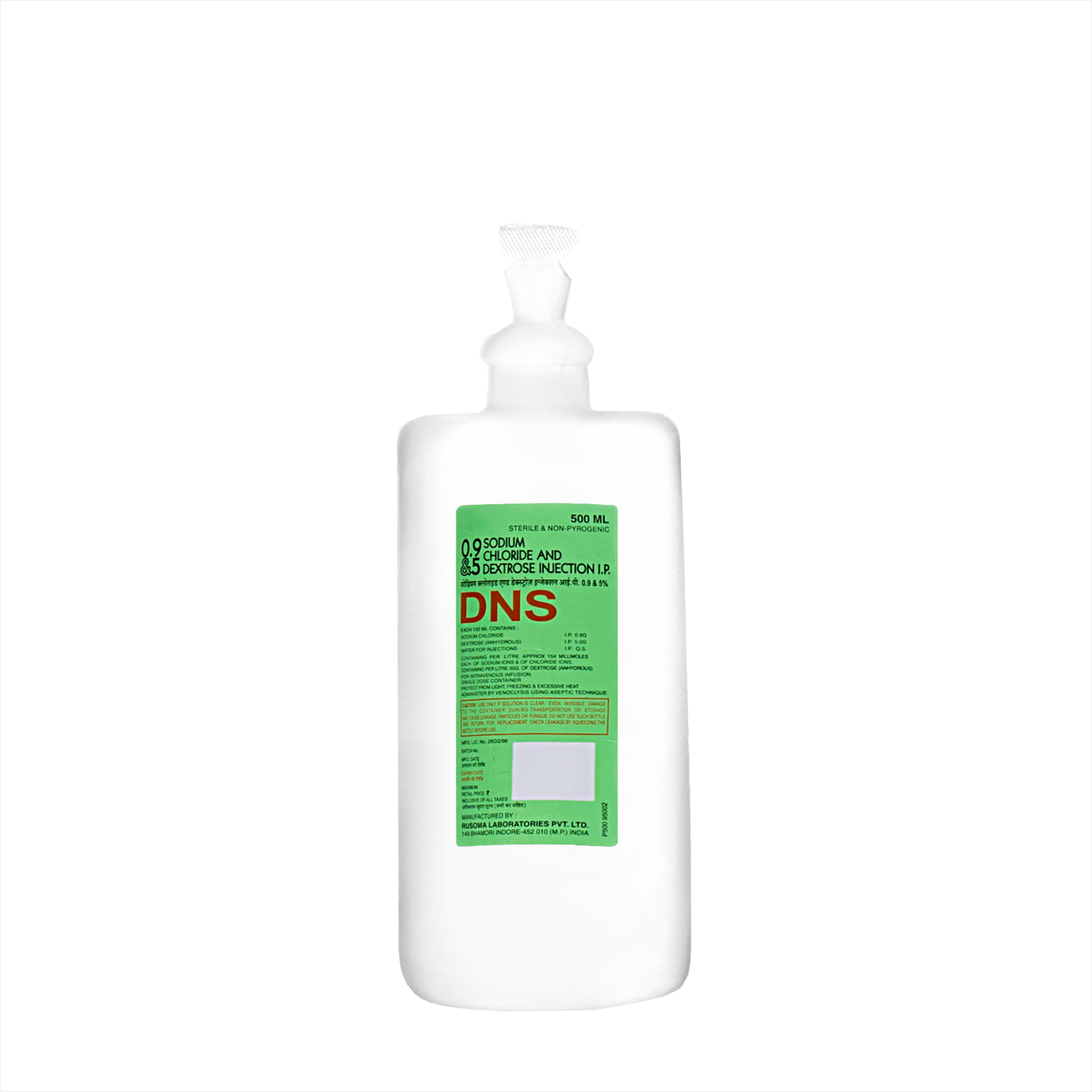
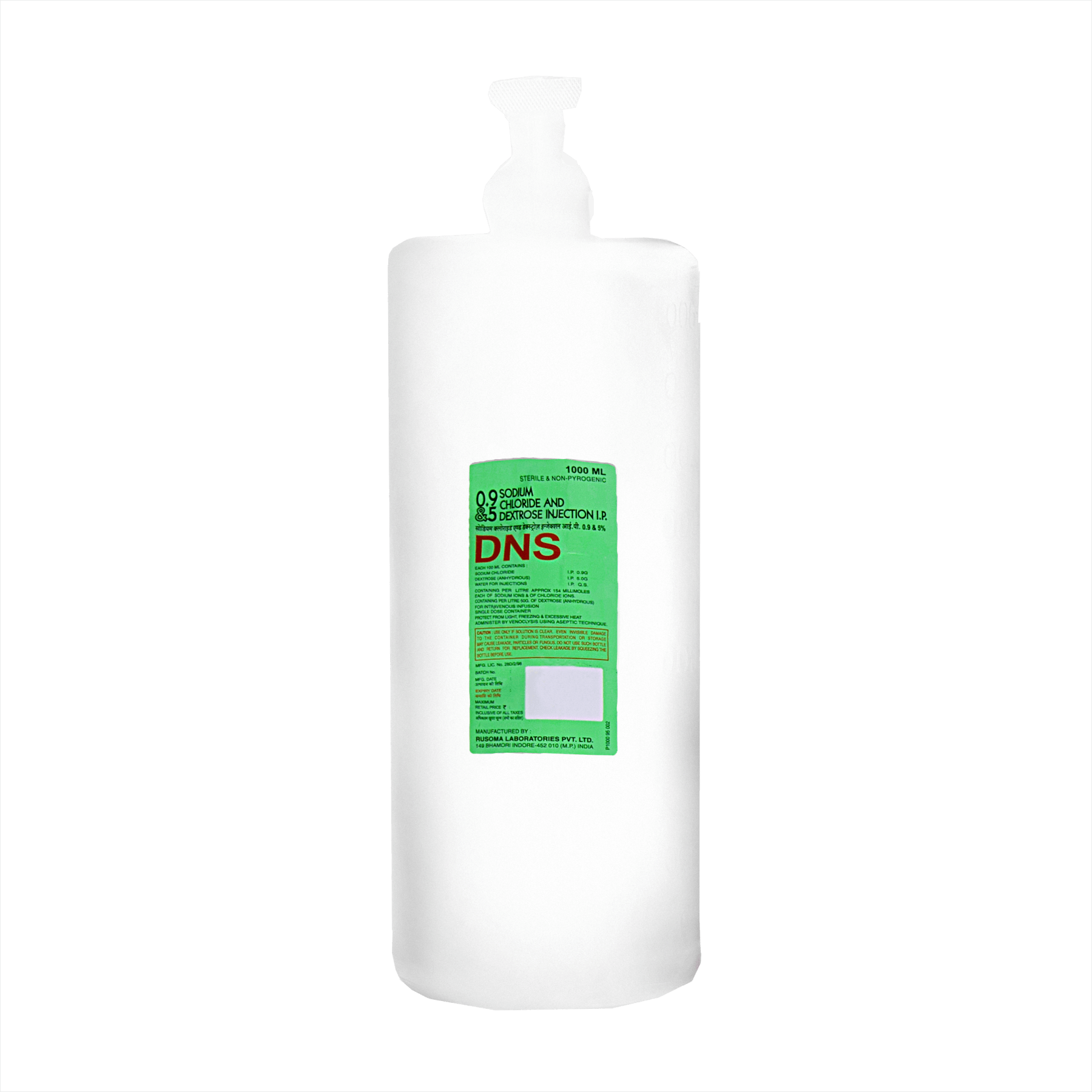

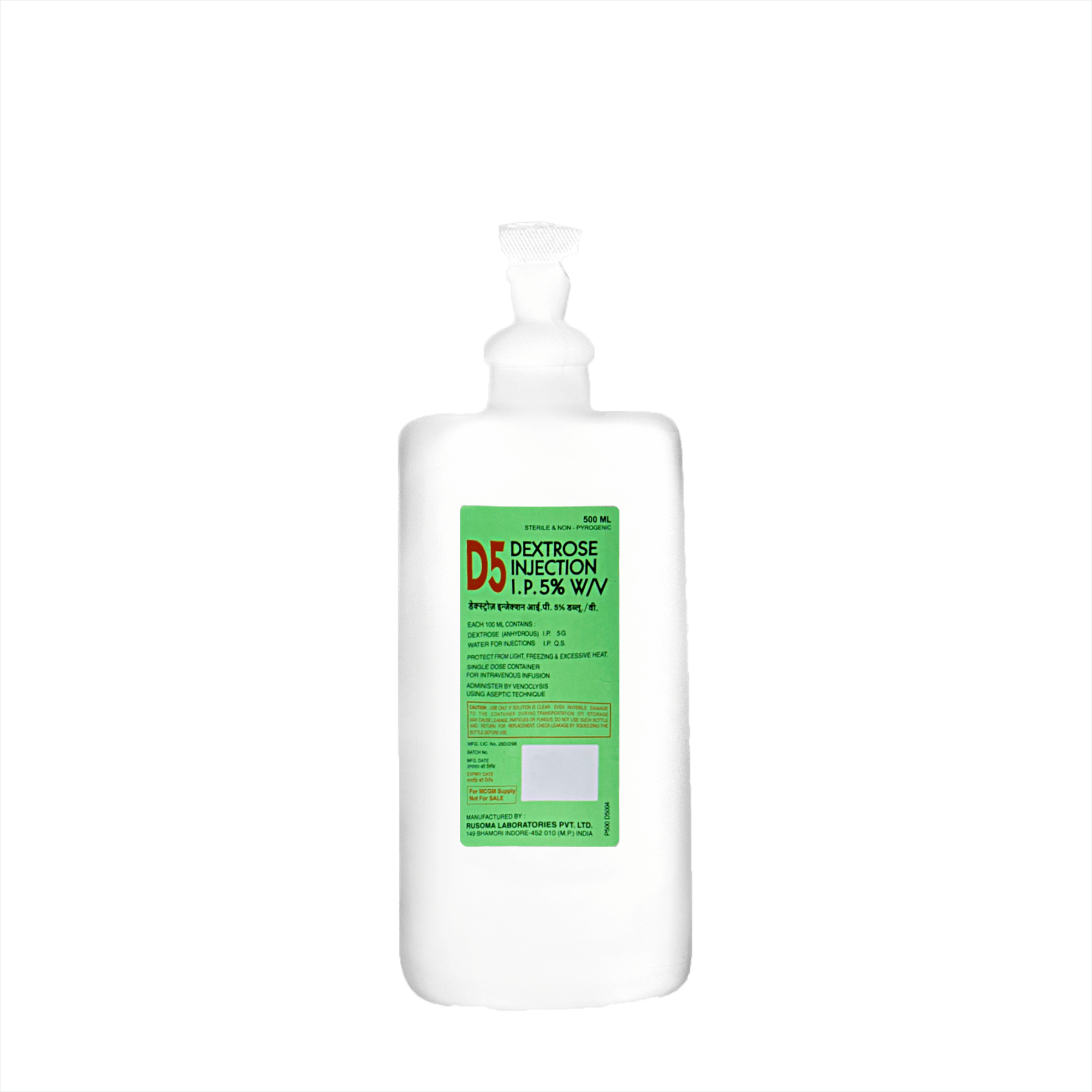
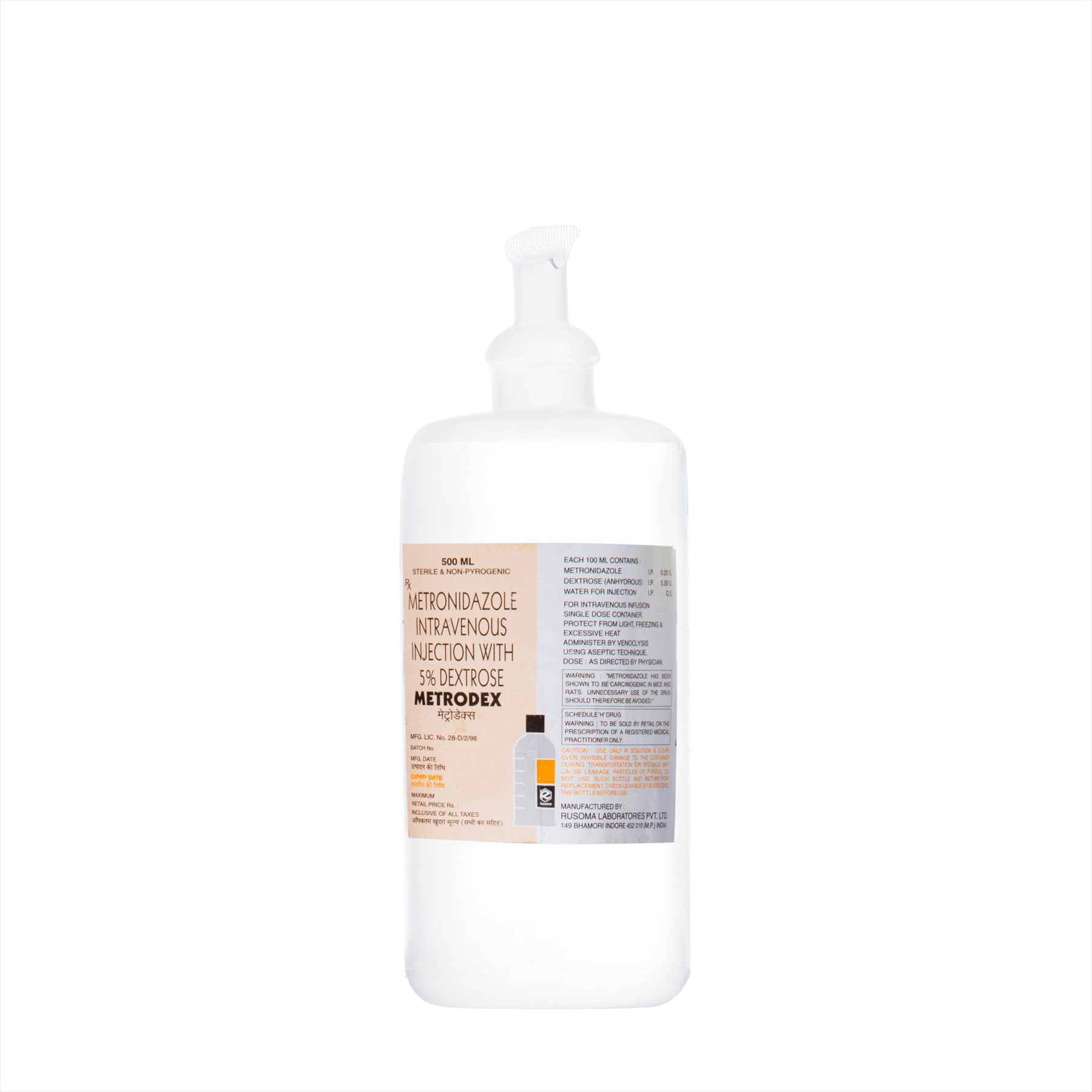
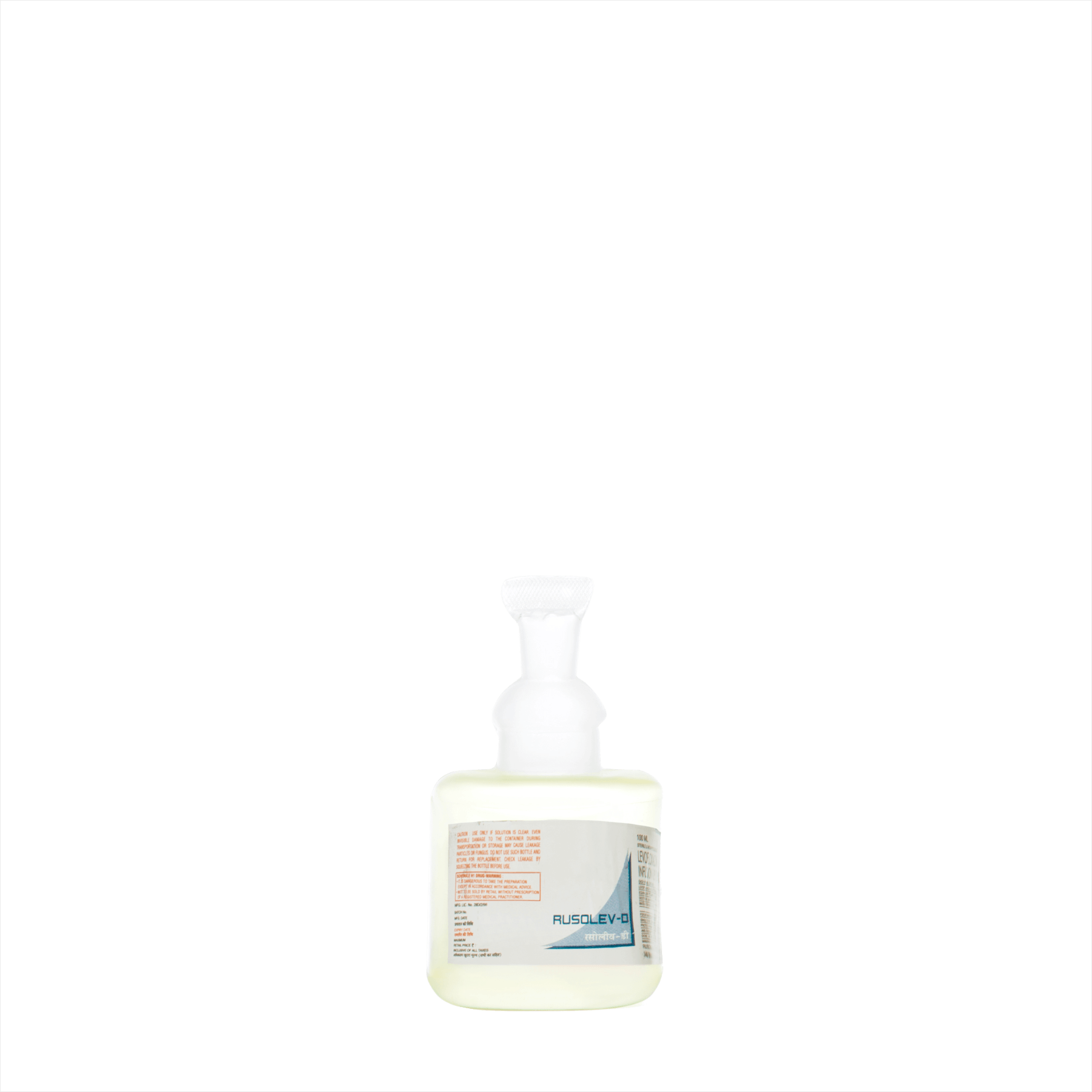
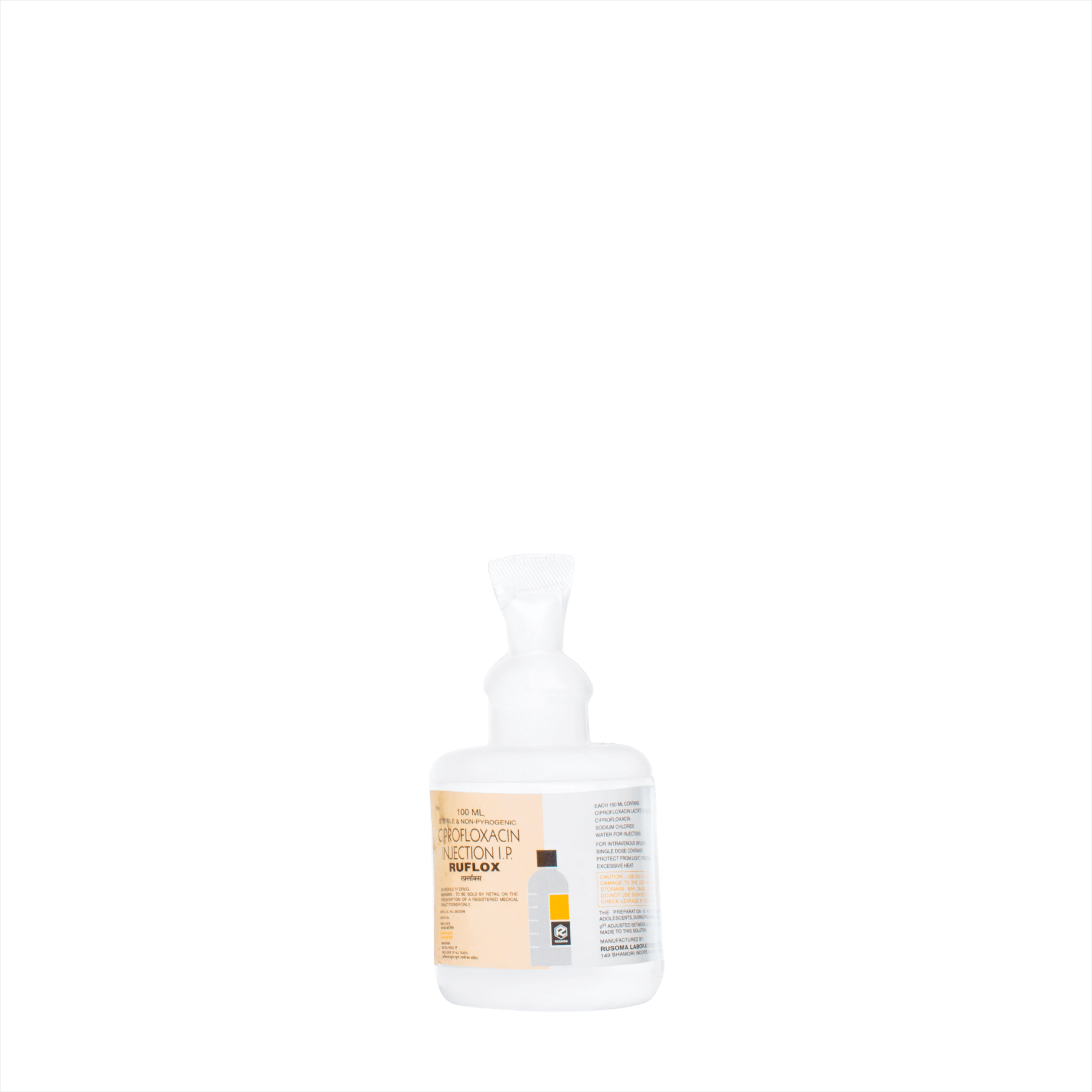
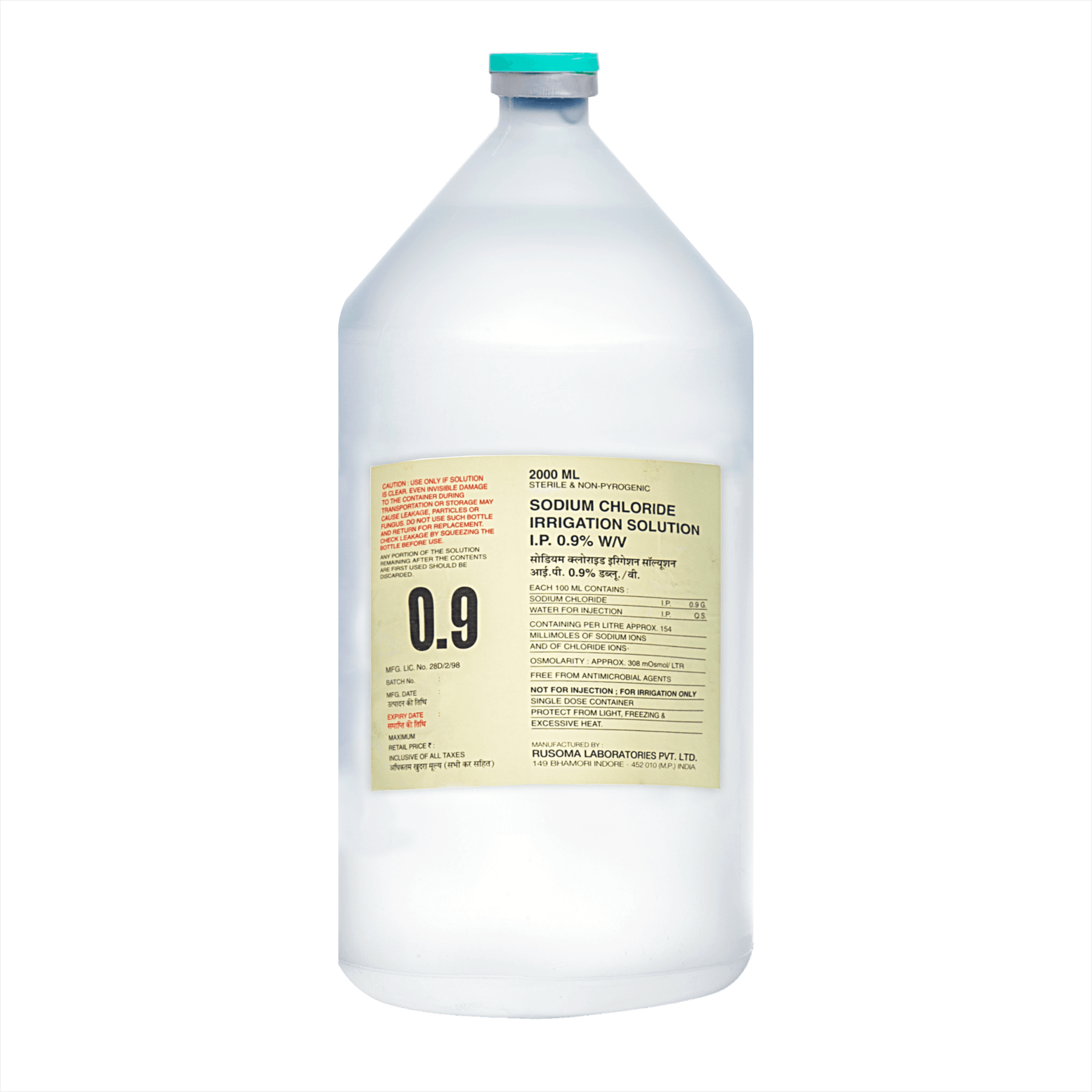
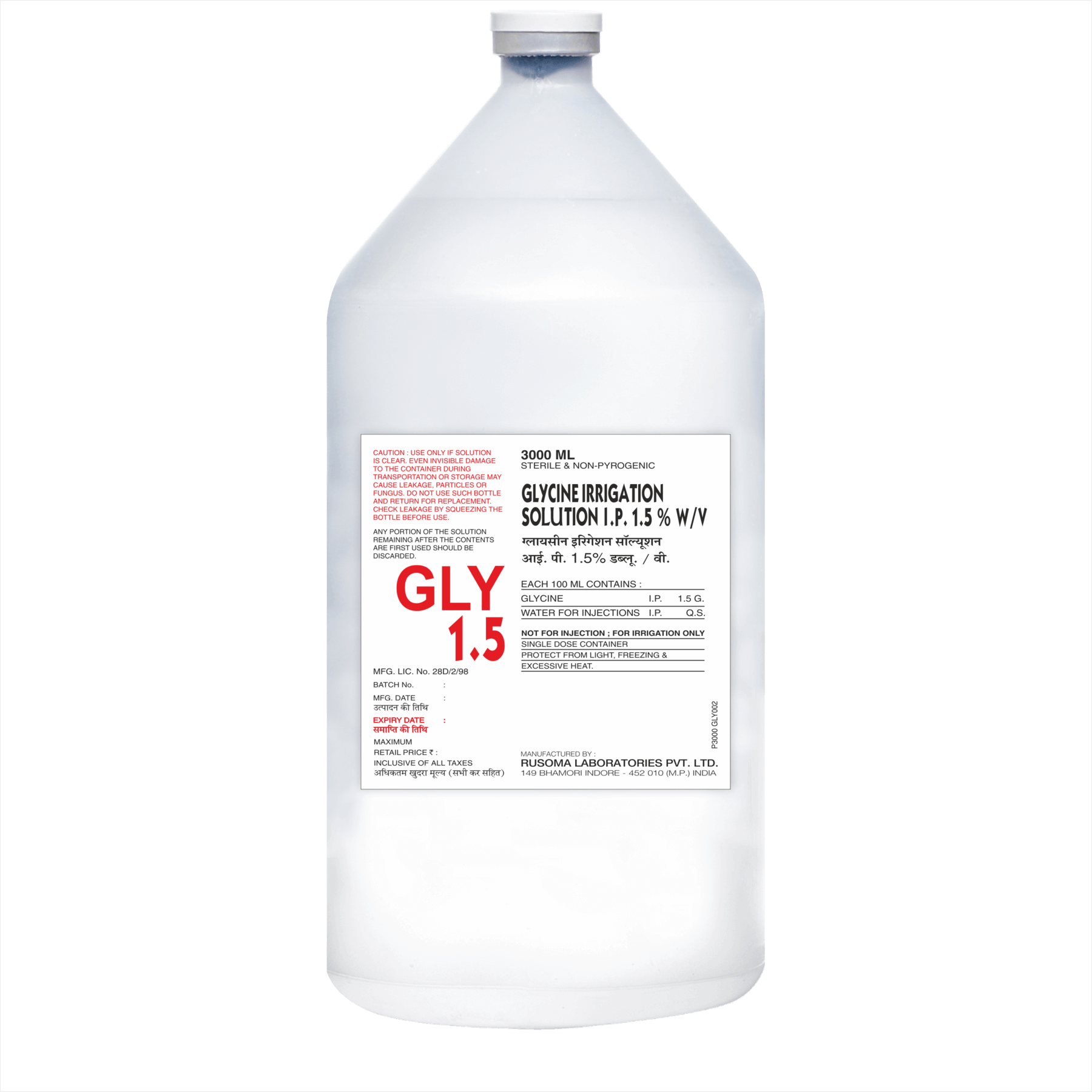
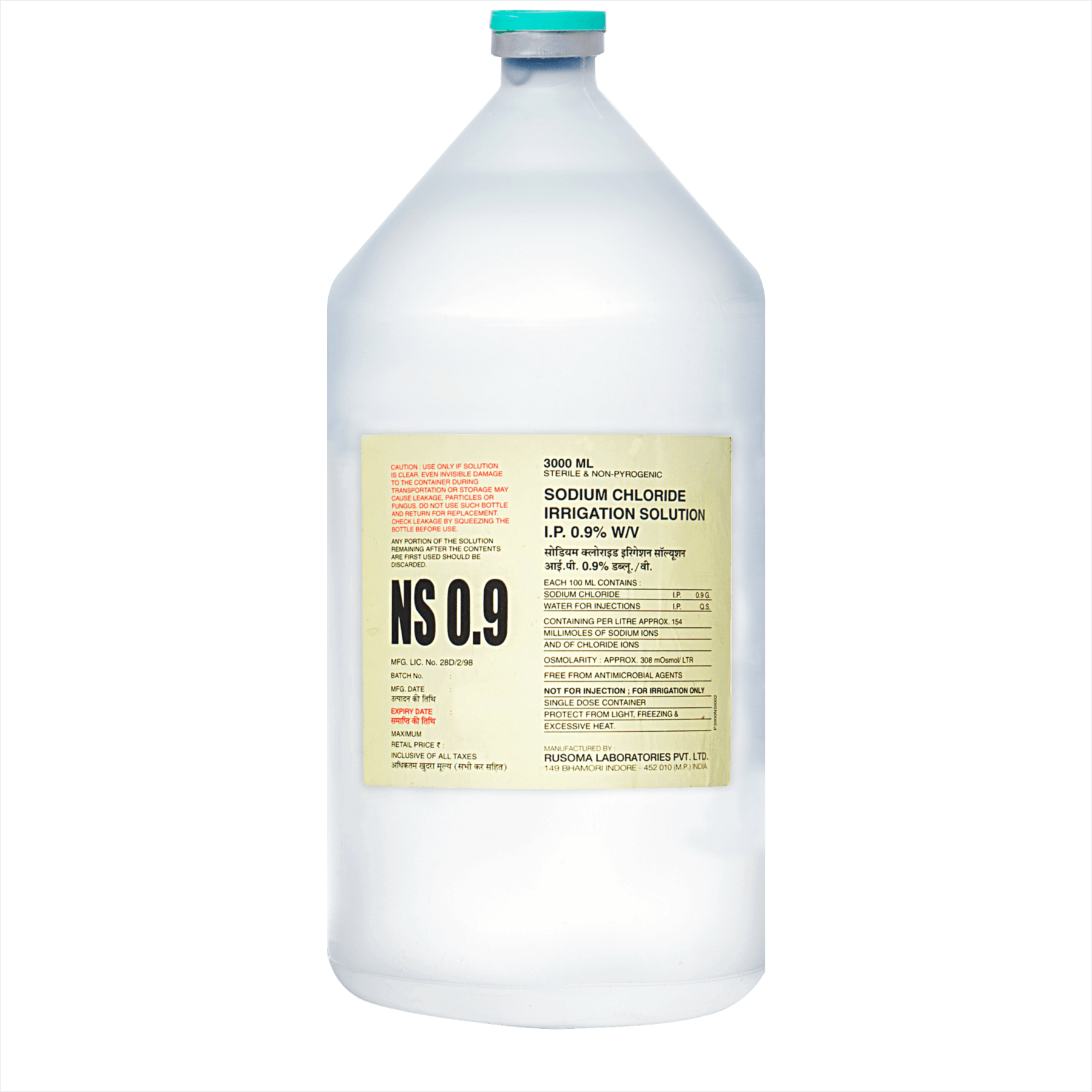
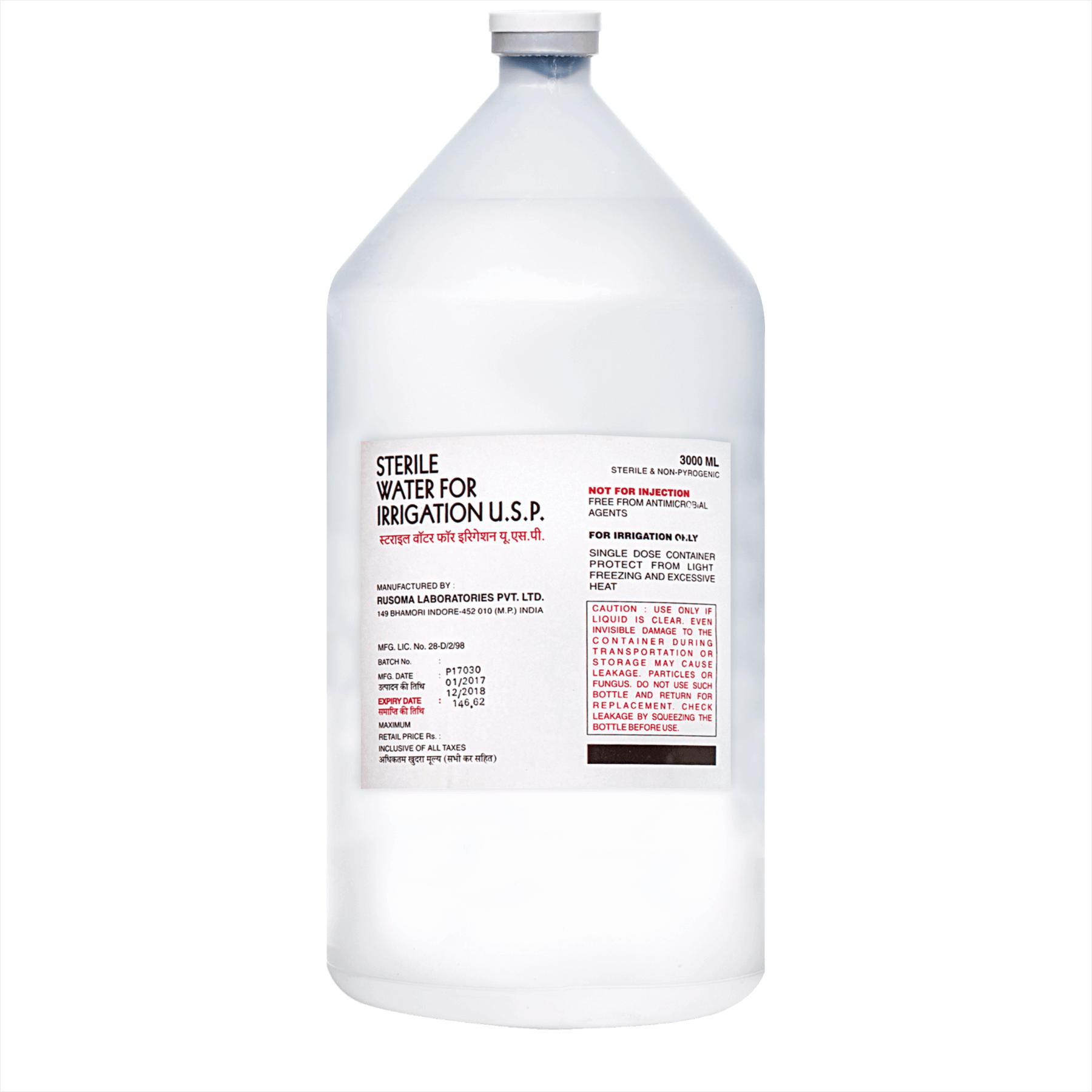
Like this post? Share it with your friends!